Energy optimisation project goes into the next phase
In a site visit to Dresden, a team from the Irish BoostUp! Europe winners Mavarick successfully implemented two IOT devices into automated guided vehicles (AGVs) to capture energy data which will be used to improve energy efficiency.
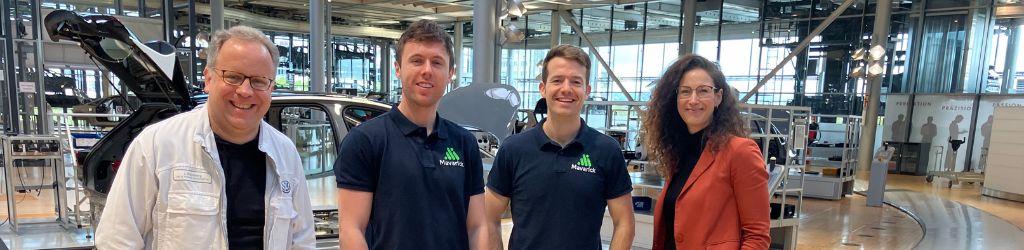
Johannes Rönsberg (VW Sachsen), Paul Byrnes, Koen Jasper (both Mavarick) and Silvia Grätz (EIT Manufacturing) met in Gläserne Manufaktur Dresden, a Volkswagen production site fully dedicated to manufacturing electric vehicles.
When Paul Byrnes and Koen Jasper opened the first automated guided vehicle in Dresden together with their counterpart colleagues from Volkswagen Sachsen, the excitement on the factory floor was tangible. Their IOT device was to be integrated into the vehicle and connected so that it can capture all energy data from the vehicle.
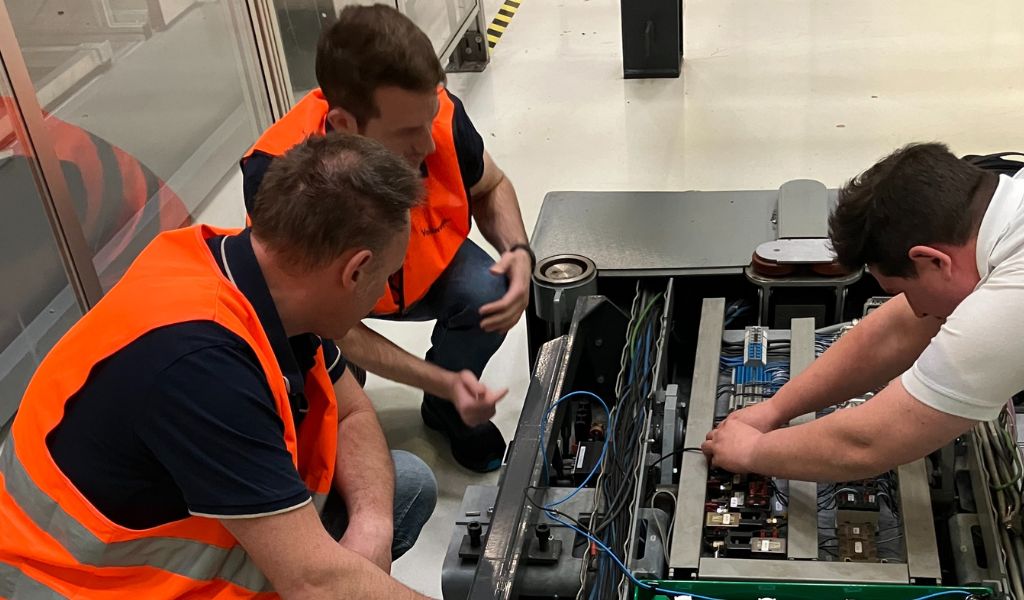
The team integrates an IOT device into an automated guided vehicle (AGV)
Once collected, this data will form the basis for optimisation: saving energy, lowering the factory’s carbon footprint, extending the AGV’s battery life, and potentially also reducing the number of AGVs and charging points.
The small device needed to fulfil some requirements, Paul Byrnes explains: “We developed an IOT device that is not invasive. To the Volkswagen team, it was very important that we leave any wiring in the AGV intact. So, we specifically developed the device to be non-invasive, light touch and lightweight.”
Planning for scalable deployment is key to ensure project success beyond the initial AGV vehicles. “The way we capture data is agnostic, that means, the process doesn’t change, regardless of the AGV type, model or make. That was very important for us, because this makes us extremely flexible.”
Once successfully in place, the edge devices were ready to transmit data. The next steps were to establish connectivity across the AGV operating space in the VW factory. “We encountered some initial connectivity challenges with the VW infrastructure,” says Johannes Rönsberg from the Volkswagen Sachsen Innovation Management. “Mavarick implemented some configuration alterations and in the end, we came up with a joint solution.”
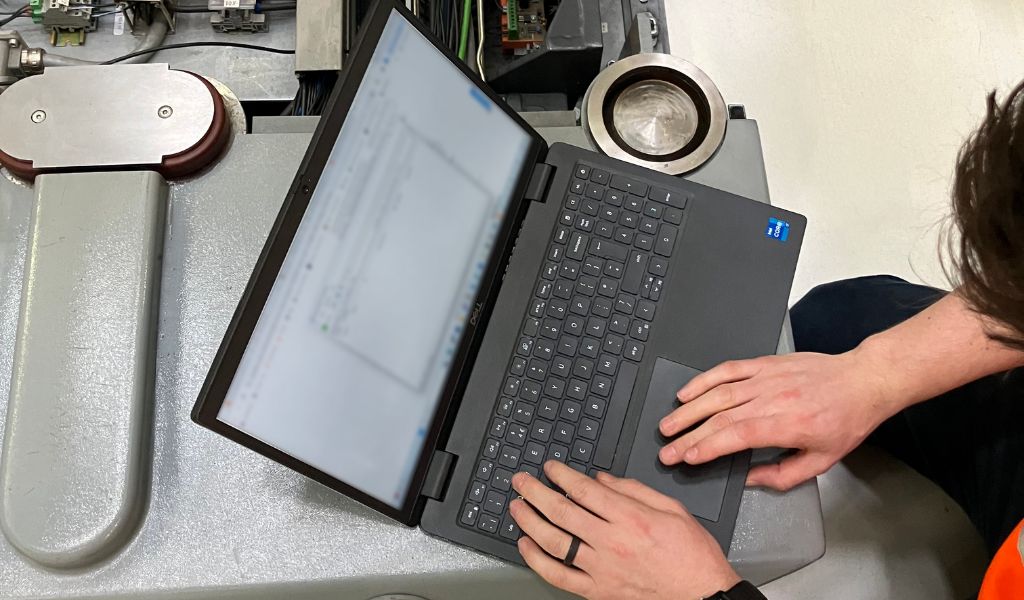
Integration complete: The IOT device transmits data.
Now connectivity has been achieved and everything is up and running – also thanks to the support of IT Project Manager Daniel Koch from the production site in Zwickau, who has supported the project from the start.
Currently, data from two AGVs which run on different circuits are being captured. “During the installation process we worked closely with Volkswagen technicians,” Koen Jasper emphasises. “This ensures that the recorded data represents the action that the AGV is taking. For example, if it was charging, if it was idle, if it was delivering a load, or whether it was driving. We were able to validate that what we were seeing from a quantitative perspective mirrored what was happening in reality. That was really, really fulfilling for both us and the Volkswagen team.”
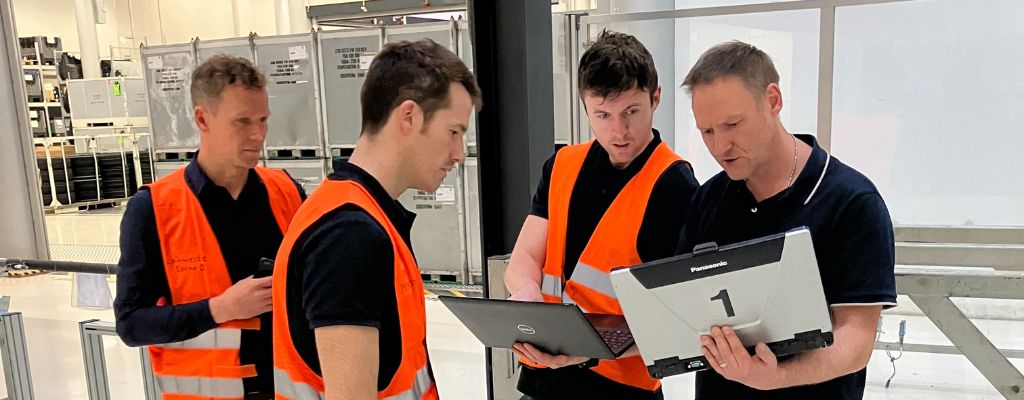
Ensuring coherence in data is key.
While the project was set out to collect data from only two AGVs, the team at Volkswagen Sachsen currently thinks about outfitting their total of 57 AGVs in the Dresden site as the installation worked so well. “We were one of the first Volkswagen factories operating with AGVs,” Dr Dirk Thieme, Head of New Mobility and Innovations at Volkswagen Sachsen explains. “The Gläserne Manufaktur Dresden was a transparent factory from the very beginning, and we were very proud about our state-of-the-art production processes with a lot of automation. Our AGVs are now 23 years old, but we are committed to bringing them into the new era of digital twins.”
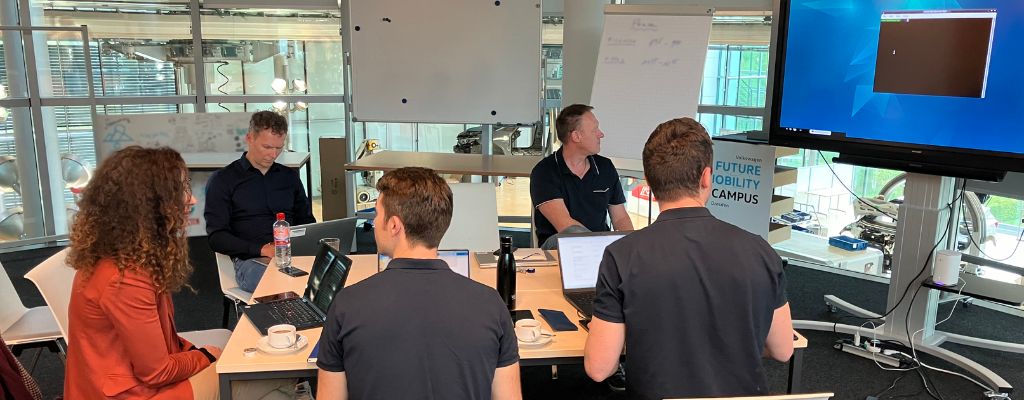
Work in progress: Coding during the site visit in Dresden
Installing the IOT devices is the first step that will enable the creation of a digital twin and integration of the digital twin into the asset administration shell which builds on industry standards set by the IDTA.
The Mavarick team has already started building out the asset administration shells (AAS) with help of AAS modelling experts from MHP, a Porsche Company, and Volkswagen Sachsen during the visit. When everybody in the team has been brought up to speed about the status of the project, these models will be finalised while the AGVs will generate data. “After a period of time, we can present the data to the team and then we can develop our analytical platform that will sit on top of the asset administration shell,” Koen Jasper outlines the next steps for Mavarick.
Project insights
Johannes Rönsberg: “We have some experience cooperating with startups it’s always amazing to see and experience the way they work. Their speed of implementing changes, their flexibility to learn from something that has not gone according to plan and their will and ability to find other ways for a solution is really impressive and it’s exactly like this with Mavarick. We’re very, very impressed with their approach and with the way they work.”
Koen Jasper: “We’ve been fortunate that EIT Manufacturing was there since the start of our journey. We were lucky enough to win BoostUp! Ireland in Mullingar and then to win the BoostUp! Europe challenge with Volkswagen and to be part of the EIT Manufacturing Summit in Brussels. For us, it’s really great that we see that there’s great value in the collaboration that we’ve been lucky enough to be engaged with a company the size of Volkswagen. And for EIT Manufacturing, the project displays to manufacturers that there’s no better place for them to pose challenges, because they get value directly from the process.”
Silvia Grätz: “We are impressed with the commitment both Mavarick and Volkswagen Sachsen show. They illustrate the recipe for success of such a project: They both invest time and human resources into the project – on the Volkswagen Sachsen side, there are specialists involved for IT and the network, for the AGVs themselves, for logistics, and not only from the Dresden site, but also from other factories. And it’s fantastic to see that VW is considering scaling the project even now, at such an early stage – this speaks volumes of the success of the project and how well the teams work together.”