Lightweight composite materials could be key to the next generation of electric vehicles
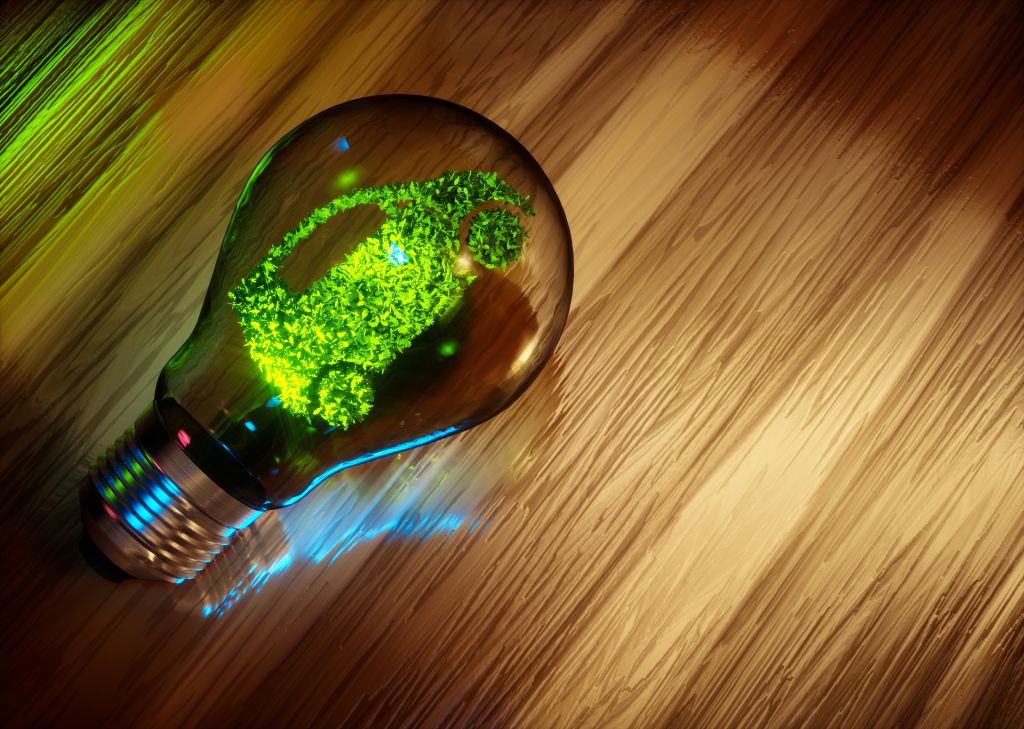
Using fibre-reinforced plastic polymers composite materials can reduce the weight of electric vehicles considerably — increasing both their range, performance, and lifespan. An ongoing project is supporting European automotive suppliers in their use of these lightweight and cost-effective composites and is providing a plan on how to integrate these materials in the circular economy.
Switching to electric vehicles is pushing car manufacturers and suppliers to adopt new technologies and ways of working, in order to boost performance and reduce the industry’s environmental footprint. Finding cost-efficient, lightweight materials and more sustainable production methods will be key factors in the race to build the electric vehicles of the future.
Building on experience from space industry
With this challenge in mind, Research Institutes of Sweden RISE together with partners University of Applied Sciences and Arts of Southern Switzerland and the Slovak University of Technology in Bratislava, set out to find ways to support existing automotive suppliers and contractors currently supplying components made of fibre-reinforced plastic polymer, also known simply as ‘composites’. Their work resulted in a project, funded by EIT Manufacturing.
“We realised that we could build on our experience of using composites in the space industry, aircraft and boats and adapt this knowledge to the automotive industry. Composites can provide several advantages: They are cost-effective to use in production and they can both cut the weight of the vehicle and increase its lifespan. Parts made of composites are also quicker, and cost-efficient to design and can lead to lower part numbers and tooling costs” said Yvonne Aitomäki, Senior Researcher at RISE Research Institutes of Sweden, who is leading the project.
As today’s electric vehicle batteries are heavy (and increase the weight of a vehicle by as much as 35%), other parts of the vehicle such as the vehicle’s suspension often need to be bulkier to handle the extra weight. But because composite components are both lighter and more robust, using composites not only cuts the weight of a specific component, it can allow manufacturers to cut the weight of other parts of the vehicle.
When combined with metal, composites are also easy to integrate into existing production lines. One effective approach used by the project is called ‘patching’.
“We are looking at how to use existing production lines and simply switch some vehicle parts traditionally made using steel with parts made of composites. It is a technique we call ‘patching’. With this way of working, you don’t have to change the production line, you just add a part made of composite instead of steel, which is both fast and cost-efficient to implement” said Yvonne Aitomäki.
Integrating composites in the supply chain
During 2020, the project has focused on collaborating with vehicle manufacturers to determine which components are needed in electric vehicles and which of these would benefit most from being produced using composites. The work has resulted in a roadmap for using composites in electric vehicle manufacturing, as well as “info nuggets”, short overviews highlighting how they can be used in production of electric vehicles.
Compared to traditional cars with gasoline or diesel engines, the production process for electric cars has not been fully optimised and there is still the possibility to affect change in order to make the production both simpler and more efficient, by integrating new materials into the production line.
Boosting composites in the circular economy
In parallel, the project team is also investigating how composite components can be incorporated into the circular economy. Focus for this part of the project has been on how to best reuse and remanufacture components. An important part of the support to suppliers has been to provide a circular business models for each component.
“There’s a huge opportunity to make composite components for electric cars that have a very long life. That is both because composites are very robust materials and electric vehicles, which have fewer moving parts than traditional vehicles, generate less wear and tear on components. Since composites are relatively simple to reuse and remanufacture, there is also the opportunity to extend the lifespans of these components even further,” said Yvonne Aitomäki.
More information on the RISE website, here: https://www.ri.se/en/what-we-do/projects/volume-automotive-composite-material-transformation