A4M – Additive for Mobility
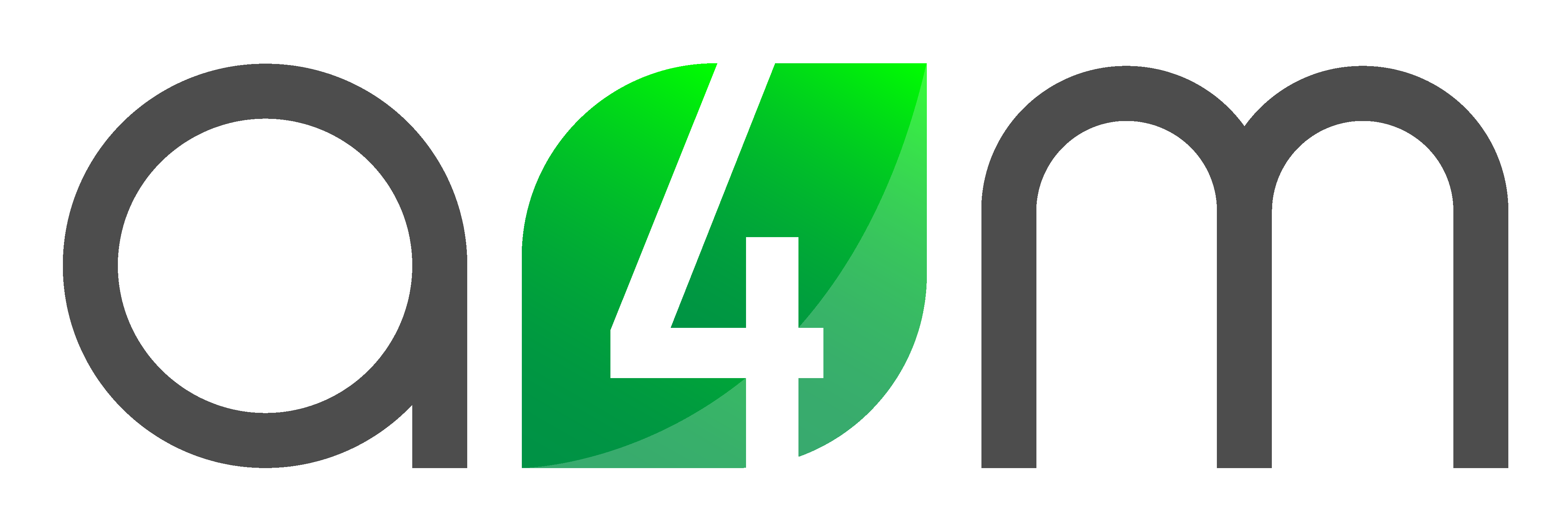
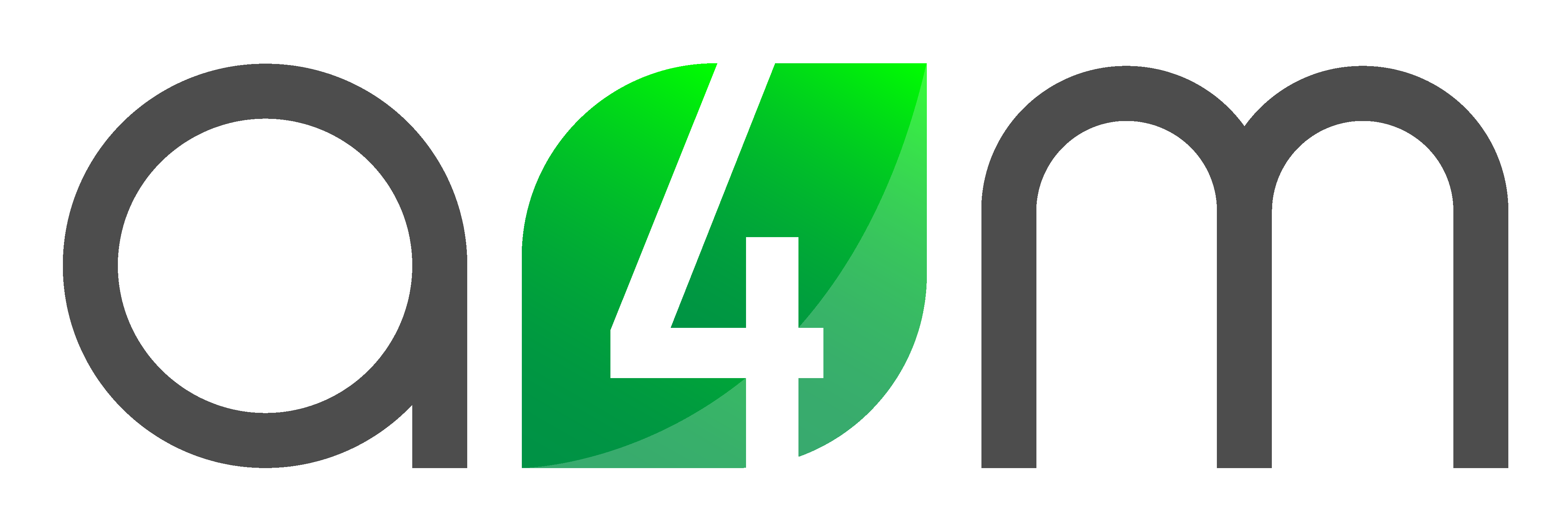
The project A4M supports the mobility transition by investigating and developing a novel, additive process chain that offers new opportunities for flexible, resilient and more sustainable series production of various components in the mobility sector (automotive, aviation, rail).
Mobility relies heavily on fossil resources for the use of vehicles, airplanes, ships and trains. In order to reduce the associated greenhouse gas emissions, various alternative technologies are currently being developed for future-oriented mobility. In this dynamic market situation of mobility change, we need suitable manufacturing systems that provide manufacturing companies with an increased degree of flexibility and resilience.
The aim of the project is to develop a flexible and resilient manufacturing system consisting of novel additive technologies of 3D sand printing (used for complex castings) and wire-based additive manufacturing (e.g. Wire Arc Additive Manufacturing, WAAM). If additive technologies are considered separately and detached from conventional manufacturing methods, various technical and economic limitations prevent further industrialisation of these promising technologies in the industry. By integrating their strengths, a new type of manufacturing system can be created that best supports the current requirements of the global mobility transition.
A new type of manufacturing cell is being developed at the IFT of TU Wien, which enables a flexible linking of the above-mentioned technologies especially for the requirements of the mobility industry (automotive, aviation, rail). Innovative technology modules developed and integrated into the cell as part of the project include multi-material connections between cast parts and additive-generated features, adaptive tool path generation and an intelligent and integrated quality assurance system. Together with industrial partners from the rail, air and surface transport sectors, selected TRL5-7 use cases on the topic of the mobility transition will be implemented in this laboratory cell and partly at the partners’ premises.
The project partners:
- Technische Universität Wien Institut für Fertigungstechnik und Photonische Technologien
- BMW Motoren GmbH
- EIT Manufacturing East GmbH
- Fill Gesellschaft m.b.H.
- Fraunhofer-Institut für Gießerei-, Composite- und Verarbeitungstechnik IGCV
- Friedrich Deutsch Metallwerk Gesellschaft m.b.H.
- Global Hydro Energy GmbH
- igm Robotersysteme AG
- MAGNA Metalforming GmbH
- ModuleWorks GmbH
- RECENDT – Research Center for Non-Destructive Testing GmbH
- Rechenraum GmbH
- RHP-Technology GmbH
- SBI GmbH
- TEST-FUCHS Aerospace Systems GmbH
- Technische Universität Wien Institut für Werkstoffwissenschaft und Werkstofftechnologie
- voestalpine Giesserei Linz GmbH
Disclaimer: This project is supported and funded by the Austrian Research Promotion Agency (FFG) under the contract number 910323.